To Skim or not to Skim……
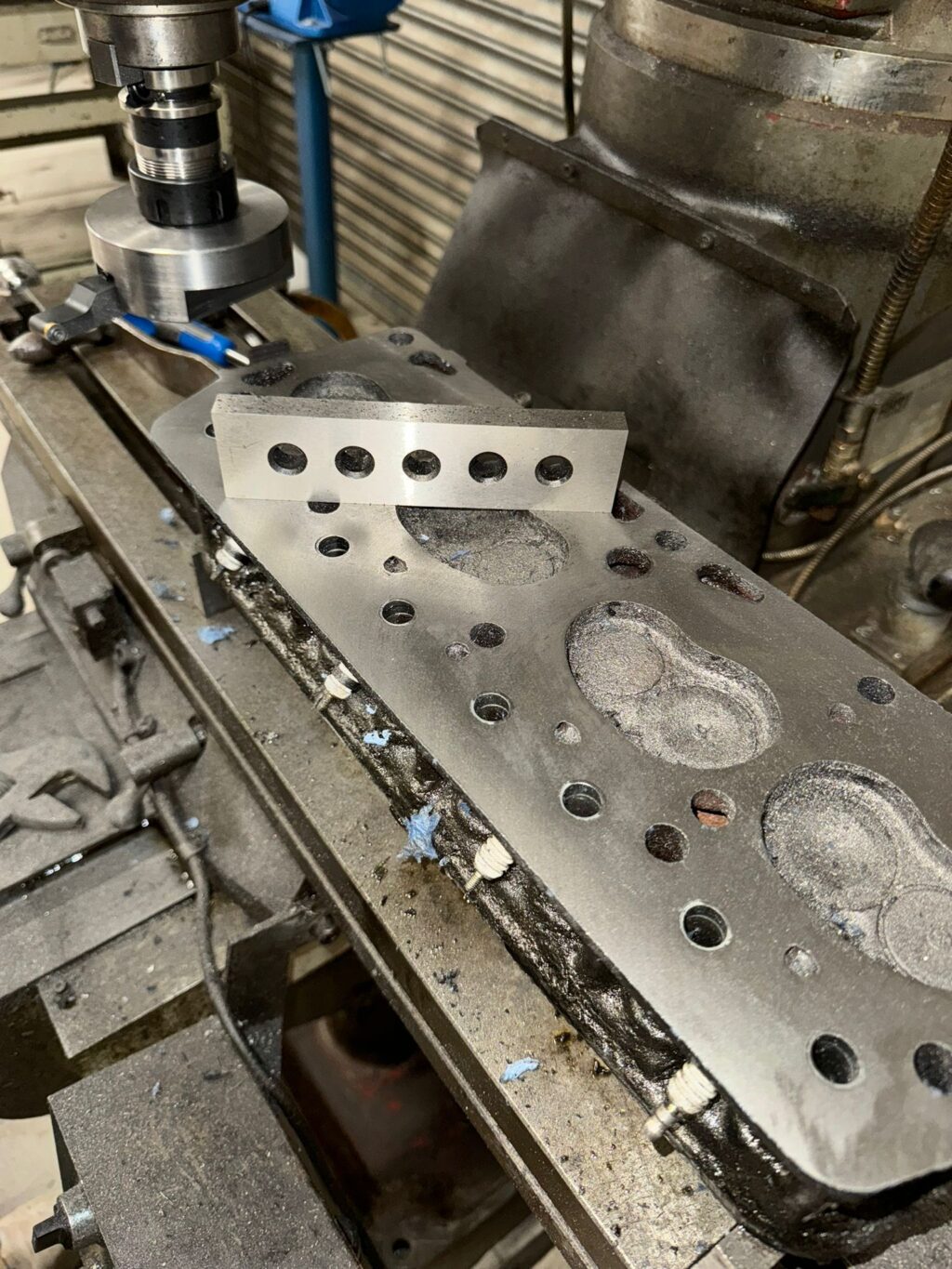
Recently we were left with a problem, our forklift had overheated and warped the cylinder head, causing the combustion gases to enter the cooling system and if you know then you know…
After looking around, drinking lots of tea and scratching heads, we decided that it would be quite a good exercise to skim the head ourselves. Problem number one.. a distinct lack of a fly cutter big enough to do the job, which created job number 1, make a fly cutter big enough to do the job….
Searching through all of our round stock, we found some 150mm god knows what steel, given the 1mm of oxidization all over it, safely say it was not stainless, but, as a lump of heavy mass, it was just the job.
We turned it down a little over 1.2mm to kill the rust and keep the mass, and then turned down a 70mm x 20mm straight shank to keep it all as one piece, idea being to use an ER32 tool holder on our mill.
Next problem, what were we to use as a cutting tool. I wanted to use some of our not so commonly used insert tooling, SRDCN will do it and give a reasonable surface finish.. For all those out there wondering, yes it did occur to us to put it on the surface grinder but where is the fun in that.
I wanted some scope for using other tooling, so I cut a slot offset from center 22mm then we could if we wanted, use 16 and 20mm insert tool holders. The tooling slot had a 10 degree rake to give the cutting tool some relief and also to ensure clearance. We then cut a slot to access the grub screw for holding the tool. Obviously this creates a shift in COG, So with some simulation (guessing a bit with the mass) we managed to get it reasonably well balanced taking some material from the opposing side.
The test phase… well we had an old Bridgeport vice that needed a bit of a clean up, so we set her with a very modest DOC and let her rip (taking cover behind our old locker) and she chooched like a charm, after a few minutes we removed ourselves from the relative safety of the locker and then watched the magic, I find it mesmerizing.
We then setup the cylinder head on some parallels and some T-Slot Machine Clamps, dialed her in (she was very very warped) and took a few passes, got her to something like good and fitted her back on, problem fixed. (We did remove and regrind the valves, replace the plugs, reset the tappets and flush the system through)
I guess the moral of the story is, we are engineers, we make some of the most complex 4/5 axis parts, although it was something outside of our comfort zone, we did it, confidence is key!
You can her in action over on our instagram https://www.instagram.com/reel/DAT8duuIRqc/?igsh=MXcxaWw4dG13NHpqOQ==